The Essential Role of Mold and Tooling in Metal Fabrication
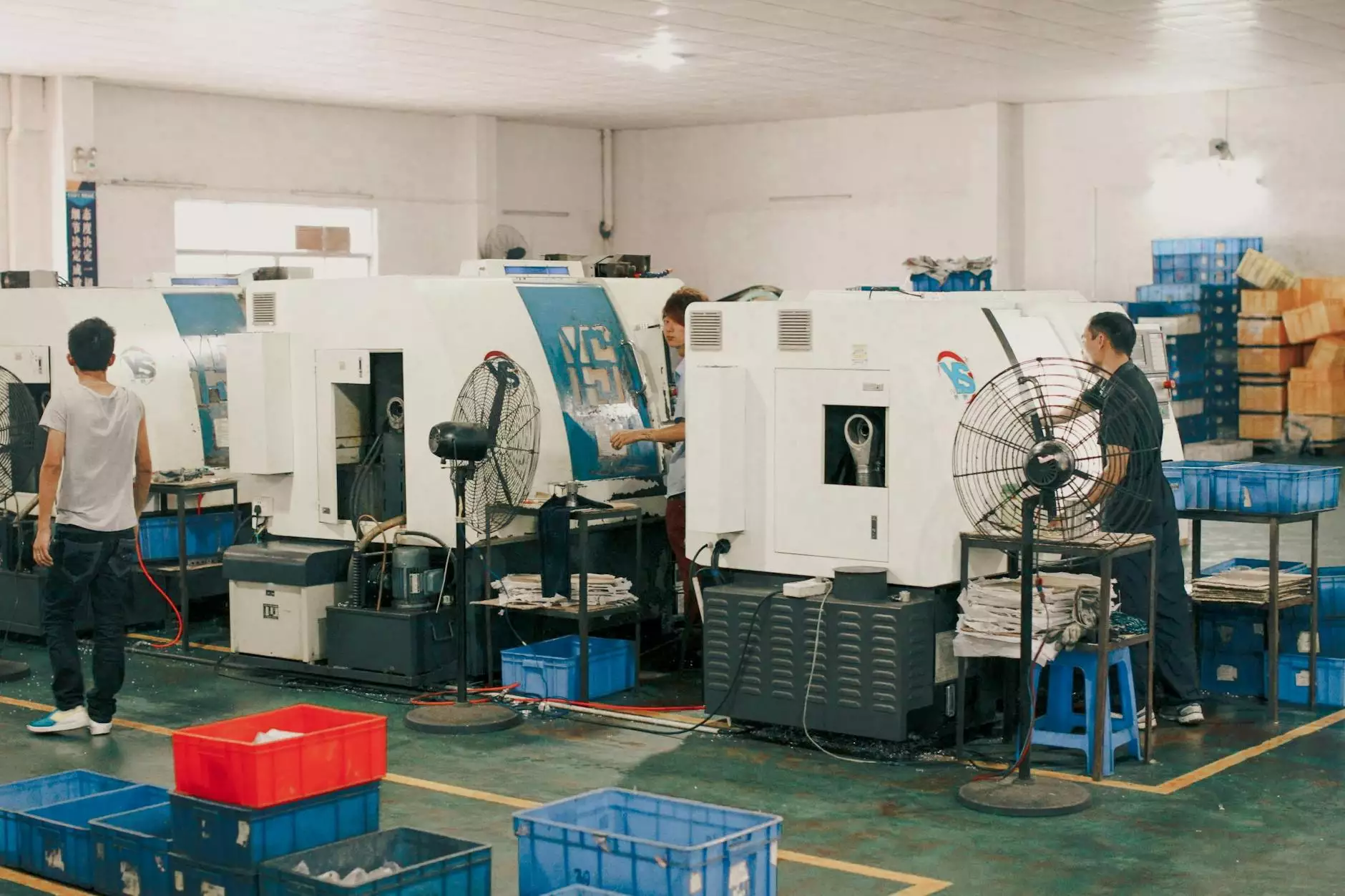
Understanding Mold and Tooling
Mold and tooling are indispensable components in the realm of manufacturing, particularly within metal fabrication. They refer to the processes and implements used to create parts and components with precision and efficiency. The importance of mold and tooling cannot be overstated, as they significantly influence the quality, accuracy, and production speed of finished products.
What is Mold?
Molds are hollow shapes used to produce parts by causing liquid material to solidify within them. In the context of metal fabrication, molds are crucial for forming various metal components. The manufacturing process involves pouring molten metal into a mold to create a specific shape once it has cooled and solidified. This technique is widely used for creating complex geometries and high-volume production runs.
The Significance of Tooling
Tooling refers to the range of tools utilized in the manufacturing process, including cutting tools, dies, and other implements necessary for shaping, cutting, and finishing metal components. Proper tooling is essential for ensuring that the machinery operates effectively and that the final product meets the required specifications and quality standards.
Applications of Mold and Tooling in Metal Fabrication
The applications of mold and tooling in metal fabrication are extensive and critical across various industries. Here are some of the prominent areas:
- Automotive Industry: Molds and tooling are used to manufacture critical components such as engine parts, body panels, and interior elements.
- Aerospace Sector: Precision-molded parts are essential for aircraft components due to strict weight and safety requirements.
- Consumer Products: Many everyday items, from appliances to electronics, rely on efficient molding processes to produce durable and aesthetically pleasing components.
- Construction Industry: Molding serves in creating structural elements and fixtures, ensuring safety and reliability in construction projects.
Benefits of High-Quality Mold and Tooling
Utilizing high-quality mold and tooling can yield numerous benefits for manufacturers, including:
- Increased Efficiency: Well-designed molds and tools reduce production time and increase throughput, leading to cost savings.
- Enhanced Quality: Precision molds provide better surface finishes and tolerances, resulting in superior product quality.
- Reduced Waste: High-quality tooling minimizes material waste during the fabrication process by ensuring accurate cutting and forming.
- Scalability: Efficient molds allow for quick adjustments to production volumes, making it easier to scale operations as demand fluctuates.
The Process of Mold and Tool Design
The design of molds and tools is a critical phase in the production process. The steps involved include:
- Requirement Analysis: Understanding the specific needs dictated by the project and intended product.
- 3D Modeling: Using CAD (Computer-Aided Design) software to create detailed 3D models of the molds and tooling.
- Simulation: Conducting simulations to assess the functioning and performance of the mold in real-world conditions.
- Prototyping: Producing a prototype to test and refine the design before full-scale production.
- Production: Finally, the approved mold is manufactured, tested, and put into operation.
Materials Used in Mold and Tooling
Mold and tooling materials play a significant role in the durability and effectiveness of the finished products. Common materials include:
- Steel: Highly durable and suitable for high-volume production; ideal for toolmaking.
- Aluminum: Lightweight and cost-effective, preferred for prototype molds and lower-volume production.
- Composite Materials: Used for specific applications requiring a balance of weight and strength.
- Thermosetting Plastics: Often used for making molds that require heat resistance and chemical stability.
Advancements in Mold and Tooling Technology
The field of mold and tooling constantly evolves, driven by technological advancements. Key innovations include:
- 3D Printing: Rapid prototyping using 3D printing techniques allows for quicker mold creation and design iteration.
- Digi-tally Controlled Machining: Enhanced precision in tooling through computer-controlled CNC machines.
- Material Science Improvements: Development of new alloys and composites that enhance mold and tooling performance.
- Software Innovations: Advanced design software that enables comprehensive simulations and real-time adjustments during the design phase.
Challenges in Mold and Tooling
While mold and tooling present numerous benefits, challenges do exist, such as:
- High Initial Costs: The investment required for high-quality molds and tools can be substantial.
- Maintenance Needs: Regular maintenance is necessary to ensure molds and tools remain effective over time.
- Design Limitations: Certain complex geometries may be challenging to reproduce accurately.
Choosing the Right Mold and Tooling Partner
When selecting a partner for mold and tooling, consider the following factors:
- Experience and Expertise: Look for a partner with a proven track record in your industry.
- Capabilities: Ensure they possess the facilities and technology to meet your specific requirements.
- Quality Assurance: Evaluate their commitment to maintaining quality standards in their manufacturing processes.
- Customer Support: Assess their willingness to provide support throughout the production process.
Conclusion
The realm of mold and tooling is fundamental to metal fabrication and has a profound impact on manufacturing processes across a multitude of industries. As technology continues to advance, the future of mold and tooling looks promising, providing manufacturers with innovative solutions that enhance efficiency, quality, and sustainability. By prioritizing high-quality mold and tooling, businesses can ensure they stay competitive in an ever-evolving market.
Get Started with DeepMould.net
If your business is ready to leverage the benefits of superior mold and tooling, consider reaching out to DeepMould.net. Our expertise in metal fabrication makes us a trusted partner in optimizing your production processes and achieving your manufacturing goals.