Understanding the Importance of a Phosphating Plant in Automotive Manufacturing
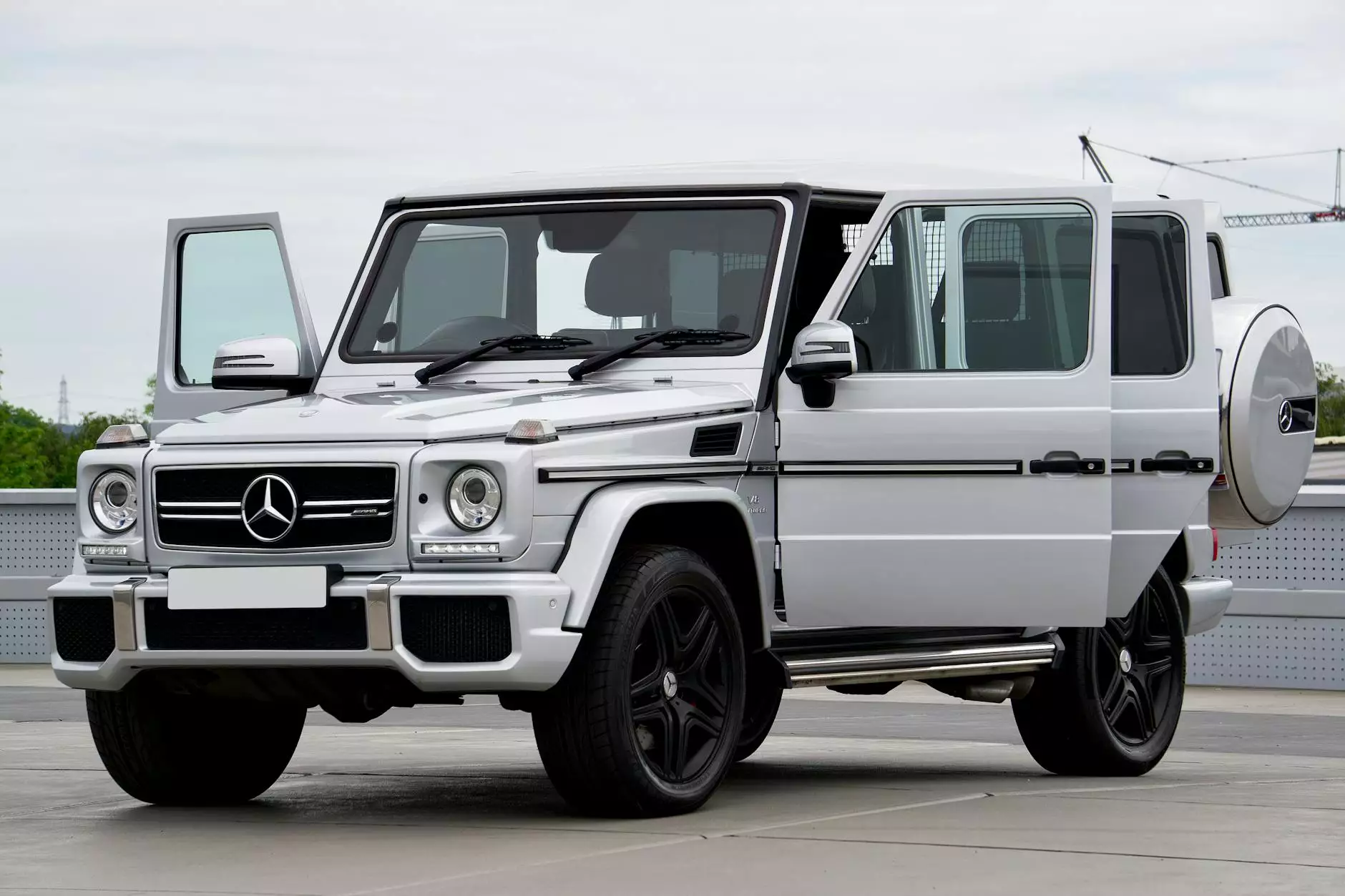
The automotive industry is highly competitive and ever-evolving. As manufacturers strive for efficiency, durability, and quality, certain processes have become essential to production lines. One such crucial process involves the use of a phosphating plant. This article delves into the intricacies of a phosphating plant, its significance in the automotive sector, and why investing in a cutting-edge phosphating facility is essential for any serious automotive manufacturer.
What is a Phosphating Plant?
A phosphating plant is a specialized facility designed for the application of a phosphate coating on metal surfaces. This surface treatment is integral for improving the properties of metals, particularly ferrous substrates. Phosphating processes enhance the performance characteristics of the materials by offering a solid foundation for subsequent coatings, such as paints and sealants.
The Phosphating Process Explained
The phosphating process involves several critical steps, all of which contribute to creating a protective, corrosion-resistant layer on the metal surface. Here is an overview of these steps:
1. Cleaning
The initial step in the phosphating process involves thoroughly cleaning the metal surfaces to remove any oils, dirt, or residues. This stage is crucial because the effectiveness of phosphating depends significantly on the cleanliness of the surface. Common cleaning methods include:
- Chemical cleaning: Utilizing alkaline cleaning agents to remove contaminants.
- Mechanical cleaning: Employing abrasive methods to ensure surface cleanliness.
2. Rinsing
After cleaning, the parts are rinsed to eliminate any cleaning agents. This step is vital as any residual chemical can negatively impact the phosphating outcome.
3. Phosphating
In this critical phase, the metal components are immersed in a phosphating solution, typically containing zinc, manganese, or iron phosphates. These chemicals react with the metal surface to form a tightly bonded phosphate layer, which serves multiple functions:
- Corrosion resistance: The phosphate layer acts as a barrier against oxidizing agents.
- Enhanced adhesion: The rough texture of the phosphate coating significantly improves the grip of paints and other coatings.
4. Rinsing Again
Subsequent to phosphating, a second rinse is performed to remove excess phosphating solution. A clean surface ensures optimal adhesion of further coatings.
5. Drying
The final step involves drying the coated components, preparing them for the next stages of manufacturing, such as painting.
Benefits of Using a Phosphating Plant
Investing in a phosphating plant offers numerous advantages that contribute to the overall efficiency and product quality of automotive manufacturing. Here are some of the principal benefits:
1. Improved Corrosion Resistance
One of the standout features of phosphating is its exceptional ability to protect metal surfaces from corrosion. In an industry where durability is paramount, the protective layer formed during the phosphating process acts as a shield against environmental factors that typically lead to oxidation.
2. Enhanced Paint Adhesion
In the automotive industry, paint adherence to the substrate is crucial for aesthetics and longevity. The phosphate coating creates a rough surface that significantly enhances the adhesion properties of subsequent paint layers. This ensures that the automotive finish remains intact even after years of exposure to harsh conditions.
3. Cost-Effectiveness
While the initial investment in a phosphating plant may be substantial, the long-term savings are undeniable. The process reduces the need for frequent re-coating and repairs, thus minimizing material wastage and labor costs associated with repainting.
4. Eco-Friendly Process
Modern phosphating plants are designed with sustainability in mind. Many utilize non-toxic and environmentally friendly chemicals. Moreover, robust waste management systems can minimize environmental impact by treating effluents before discharge.
5. Increased Production Efficiency
The integration of a phosphating plant within the automotive manufacturing process streamlines production. With each step carefully controlled, manufacturers can achieve consistent quality, reduce cycle times, and meet strict production schedules.
Applications of Phosphating in the Automotive Industry
The versatility of phosphating is evident in its wide range of applications within the automotive sector. Here are some typical uses:
1. Car Body Panels
Car body panels often undergo phosphating treatment before painting to ensure long-lasting durability and resistance to rust and wear.
2. Engine Components
Phosphating is used on engine parts to prevent oxidation and enhance the adhesion of protective coatings that ensure performance and longevity.
3. Chassis and Underbody Parts
Due to their exposure to harsh environmental conditions, chassis and underbody components benefit greatly from phosphating, providing a robust protective layer against corrosive elements.
4. Fasteners and Small Parts
Small components such as bolts and nuts are often phosphated to maintain their integrity and performance, particularly in high-stress applications.
Choosing the Right Phosphating Plant for Your Needs
When considering the implementation of a phosphating plant, automotive manufacturers must weigh several factors to ensure they select a facility that meets their operational needs and quality standards. Here are some key considerations:
1. Capacity and Automation
The capacity of the phosphating plant should align with the production demands of the automotive facility. Additionally, an automated phosphating line can significantly increase efficiency and consistency.
2. Technology and Equipment
Invest in modern phosphating technology that employs efficient chemical usage and energy consumption. Systems that use less water and chemicals for rinsing can enhance sustainability.
3. Compliance with Standards
Ensure the phosphating plant complies with local and international environmental standards. Adherence to these regulations safeguards the company’s reputation and avoids potential fines.
4. Support and Maintenance
Select a supplier that provides ongoing support and maintenance to address any challenges that may arise post-installation. This ensures minimal downtime and smooth operations.
Conclusion
In conclusion, a phosphating plant is not just a luxury but a necessity for automotive manufacturers aiming to enhance product quality and longevity. The phosphating process offers profound benefits, such as improved corrosion resistance and paint adhesion while also being cost-effective and environmentally friendly. As the automotive industry continues to grow and evolve, investing in advanced phosphating technology will undoubtedly provide a competitive edge and contribute to sustainable manufacturing practices. Organizations like Autocoat India are at the forefront of providing innovative solutions in the automotive paint and phosphating sectors, ensuring manufacturers get the best potential from their production lines.