Understanding the Importance of Mold and Tooling in Metal Fabrication
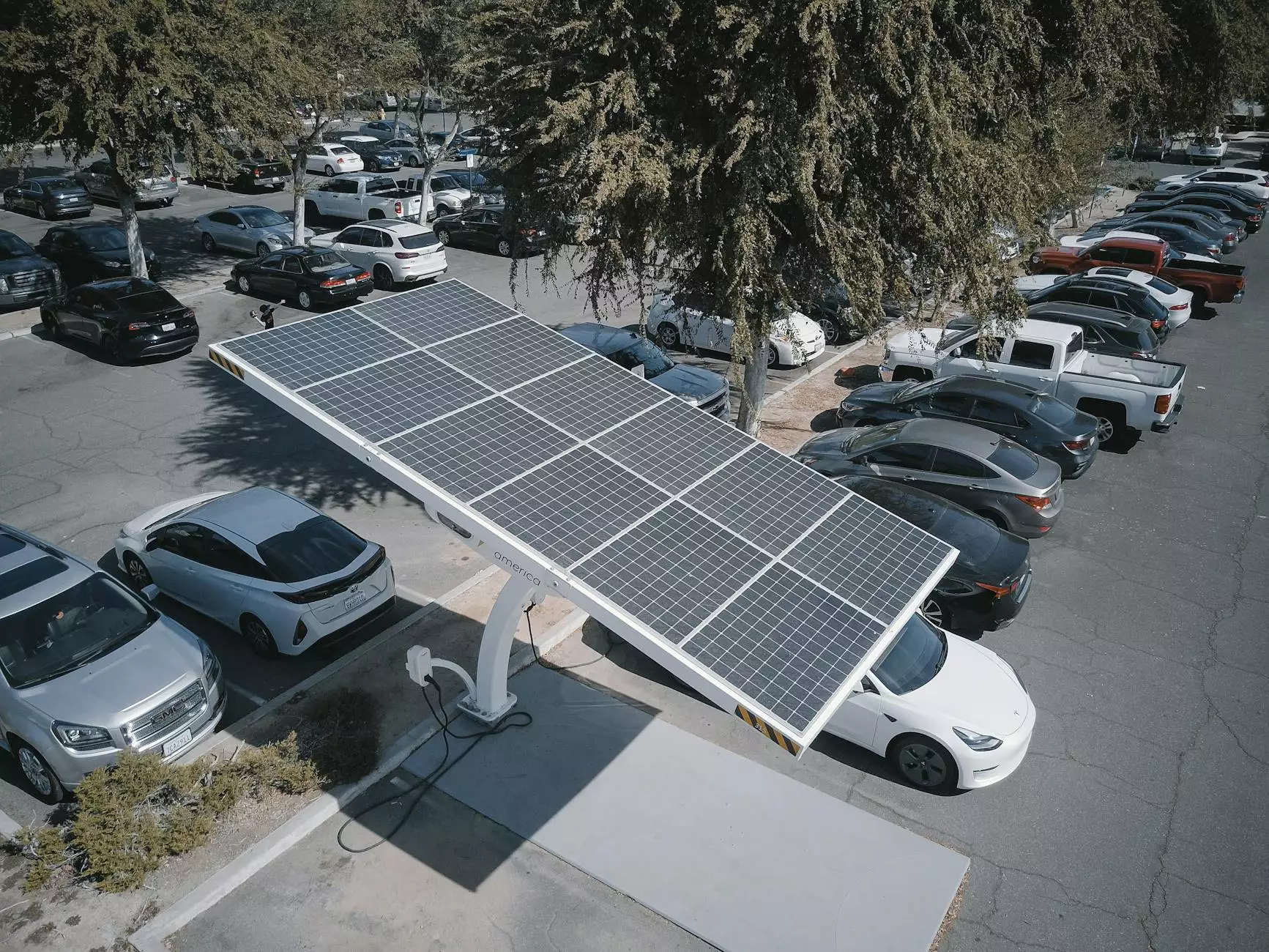
The Evolution of Mold and Tooling
Mold and tooling technologies have undergone significant transformations over the years, impacting various industries, particularly in metal fabrication. At the heart of industrial manufacturing, mold and tooling facilitate efficient, precise production processes that meet the growing demands of today’s market.
The history of mold and tooling dates back centuries, but it has rapidly advanced with the advent of modern technologies such as computer-aided design (CAD), 3D printing, and advanced materials. These innovations have allowed businesses to realize faster production cycles, improved quality, and reduced costs.
What is Mold and Tooling?
In manufacturing, mold and tooling refer to the processes and equipment used to create parts and products from various materials. Molds create cavities into which materials—such as metals, plastics, or ceramics—are introduced to form specified shapes. Tooling, on the other hand, encompasses the tools and machinery used to work with materials during production.
Types of Molds
- Injection Molds: Used primarily for plastics, this method involves injecting molten material into a mold cavity.
- Blow Molds: Ideal for hollow objects, blow molds create shapes by using air pressure.
- Compression Molds: Utilized for various materials, compression molds involve placing material in a heated mold and applying pressure to shape it.
Key Tooling Techniques
- Machining: This process includes cutting, grinding, and drilling to achieve detailed designs.
- 3D Printing: A revolutionary method that fabricates parts layer by layer using digital models.
- Forming: Techniques like stamping and bending that reshape materials through mechanical forces.
The Benefits of Advanced Mold and Tooling Practices
Implementing sophisticated mold and tooling processes offers numerous advantages for businesses in metal fabrication:
1. Cost Efficiency
Accurate molds and tools reduce material waste, lower production costs, and minimize the need for rework. By refining these processes, companies can enjoy substantial savings that contribute to a healthier bottom line.
2. Enhanced Quality Control
Modern tooling methods, such as CNC machining, ensure precision in product manufacturing. This enhanced quality control leads to fewer defects, ensuring products meet stringent specifications and customer expectations.
3. Speed and Efficiency
Advanced mold-making technologies facilitate quicker setup times, allowing businesses to respond rapidly to market demands. This agility is critical in a competitive landscape.
4. Flexibility in Design
Mold and tooling innovations enable manufacturers to create a broader range of designs and prototypes without extensive lead times. This flexibility supports custom orders and short production runs, aligning with modern consumer trends.
How Deepmould.net Stands Out in the Mold and Tooling Industry
At deepmould.net, we pride ourselves on delivering cutting-edge solutions that elevate the mold and tooling processes for our clients in the metal fabrication sector. Our expertise in mold and tooling, combined with a commitment to innovation, sets us apart from the competition.
Why Choose Deepmould.net?
- Expert Team: Our experienced professionals bring extensive knowledge and skills in mold design and manufacturing.
- State-of-the-Art Technology: We utilize the latest technologies to ensure high-performance and reliable tooling solutions.
- Customer-Centric Approach: Understanding our clients' unique requirements allows us to tailor our services and provide exceptional support.
- Sustainability: We are dedicated to environmentally responsible practices, incorporating sustainable materials and processes into our operations.
Future Trends in Mold and Tooling
The mold and tooling industry is continuously evolving, driven by technological advancements and changing market demands. Here are some key trends that are shaping the future:
1. Automation and Industry 4.0
As the industry embraces Industry 4.0, businesses are increasingly integrating automation and smart technologies into their mold and tooling processes. This results in improved efficiency, predictive maintenance, and enhanced data analytics.
2. Sustainability Initiatives
With a growing emphasis on sustainability, companies are seeking eco-friendly materials and processes. Solutions such as recyclable mold materials and energy-efficient manufacturing practices are gaining traction.
3. Increased Customization
Consumers are demanding more personalized products, leading to a rise in custom mold and tooling solutions. Advanced technologies will enable greater design flexibility and faster turnaround times for bespoke manufacturing.
4. Integration of Augmented Reality (AR)
Augmented reality is set to revolutionize mold design and tooling processes, allowing designers to visualize projects in a 3D space before production, thereby enhancing accuracy and reducing iterations.
Conclusion: The Path Forward in Mold and Tooling
In conclusion, the realm of mold and tooling stands as a cornerstone of metal fabrication, profoundly impacting production efficiency, product quality, and cost-effectiveness. As the industry evolves with advanced technologies, staying informed and adaptable will be crucial for businesses seeking to maintain a competitive edge.
At deepmould.net, we are committed to navigating the future of mold and tooling, harnessing innovative solutions that not only meet but exceed our clients' expectations. Whether you are a startup or a seasoned manufacturer, we are here to assist you in mastering the art of mold and tooling for your business success.
© 2023 Deep Mould. All rights reserved.