Understanding Auto Injection Molding
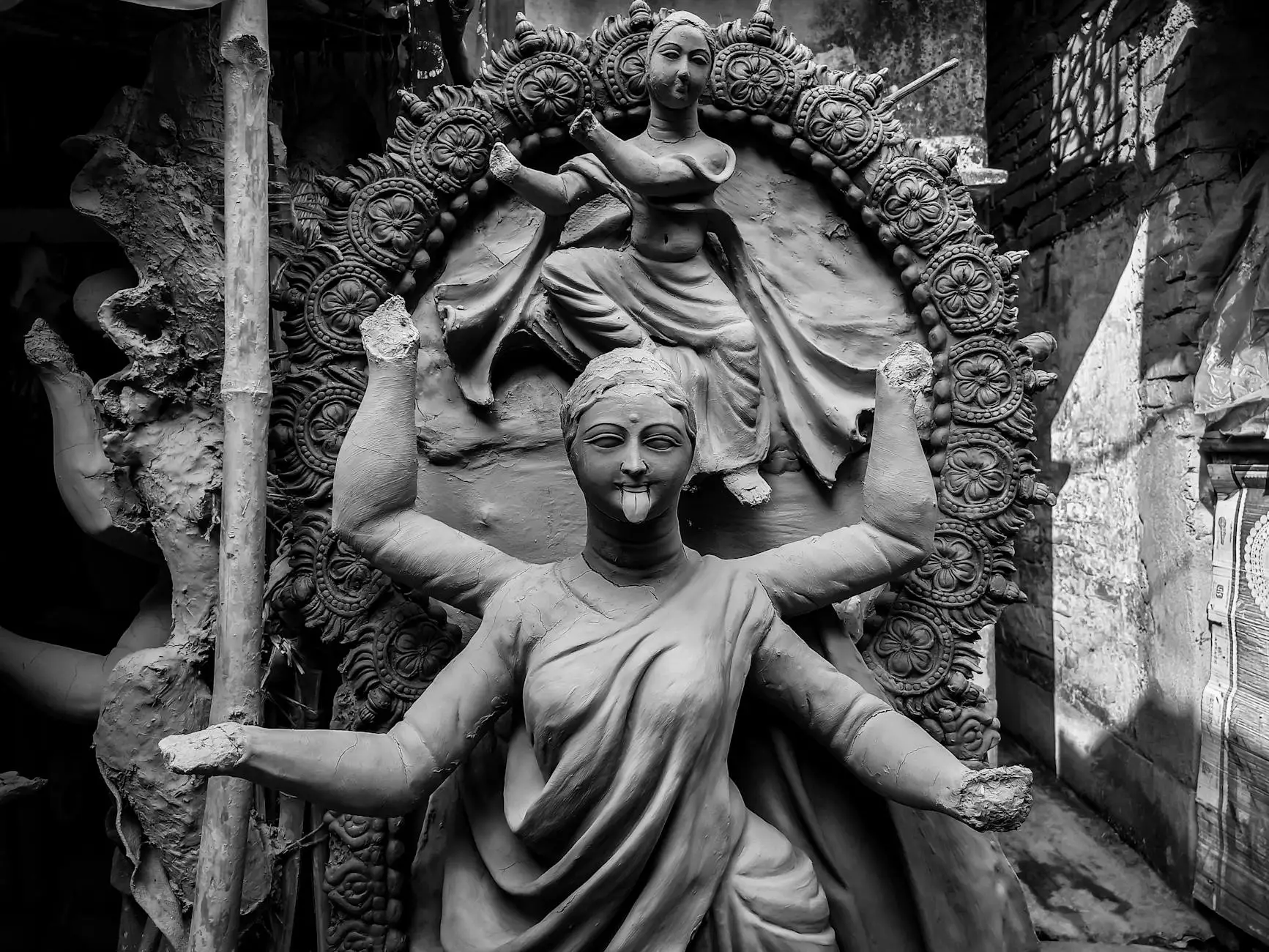
Auto injection molding is a cutting-edge manufacturing process that plays a critical role in the production of plastic parts and components. This technique is particularly significant for industries that require high precision, consistency, and efficiency in their manufacturing practices. In simple terms, auto injection molding involves the injection of molten material into a mold to create various products ranging from simple components to complex assemblies.
How Auto Injection Molding Works
The process begins with the preparation of the mold, which is usually crafted from steel or aluminum. Here’s a more detailed breakdown of the steps involved in auto injection molding:
- Material Selection: The appropriate thermoplastic or thermosetting material is selected based on the desired properties of the final product.
- Melting: The chosen material is heated to a temperature where it becomes malleable.
- Injection: The molten material is injected into a precision-engineered mold at high pressure.
- Cooling: Once the mold is filled, it is cooled down to allow the material to solidify.
- Demolding: After cooling, the final product is removed from the mold, often requiring minimal finishing work.
The Advantages of Auto Injection Molding
Auto injection molding offers numerous advantages over traditional manufacturing techniques, making it a preferred method for many businesses. Some of the key benefits include:
- High Efficiency: The speed of production is unparalleled, allowing for rapid manufacturing of large quantities of parts.
- Consistency: Automated processes minimize human error, resulting in uniformity in product quality and dimensions.
- Complex Geometries: The capability to produce intricate designs that may be difficult or impossible to achieve through other methods.
- Cost-Effectiveness: While the initial setup costs may be high, the long-term savings from reduced production time and waste make it economically viable.
- Material Versatility: A wide variety of materials can be used, allowing for customized solutions based on project requirements.
Applications of Auto Injection Molding in Metal Fabrication
In the context of the metal fabrication industry, particularly businesses like DeepMould.net, auto injection molding has various applications:
1. Automotive Industry
Auto injection molding is extensively used to produce various automotive components such as dashboard panels, bumpers, and fuel tanks. The precision and durability of molded parts ensure safety and reliability in vehicles.
2. Electronics
Many electronic devices rely on auto injection molded components for casings, connectors, and insulators. The process allows for the production of lightweight and compact parts while maintaining high performance.
3. Consumer Products
Everyday items like containers, toys, and appliances utilize components produced through auto injection molding. The ability to mold complex shapes makes it ideal for consumer goods.
Challenges in Auto Injection Molding
While the benefits are significant, there are challenges faced by manufacturers in auto injection molding:
- High Initial Costs: The setup costs for molds and machinery can be substantial, which may deter smaller businesses.
- Material Limitations: Not all materials are suitable for injection molding, which can limit design options.
- Maintenance and Repair: The machinery and molds require regular maintenance and can be costly to repair.
Future Trends in Auto Injection Molding
The landscape of auto injection molding continues to evolve with advancements in technology. Here are some future trends to watch for:
- Sustainability: Increased focus on eco-friendly materials and processes to reduce environmental impact.
- Smart Manufacturing: Integration of IoT and AI in production processes to enhance efficiency and reduce downtime.
- 3D Printing Synergizing: Combining traditional injection molding with 3D printing technologies for rapid prototyping and production.
Conclusion
In conclusion, auto injection molding represents a vital aspect of modern manufacturing, particularly within the metal fabrication sector. It streamlines production, enhances product quality, and enables businesses to meet the increasing demands of consumers. As companies like DeepMould.net leverage this technology, they are not just improving their operational capabilities, but also setting standards for the future of manufacturing. Staying abreast of industry trends and technological advancements will be crucial for businesses looking to maintain a competitive edge in this dynamic landscape.