CNC Precision Machining Suppliers: Elevating Manufacturing Standards
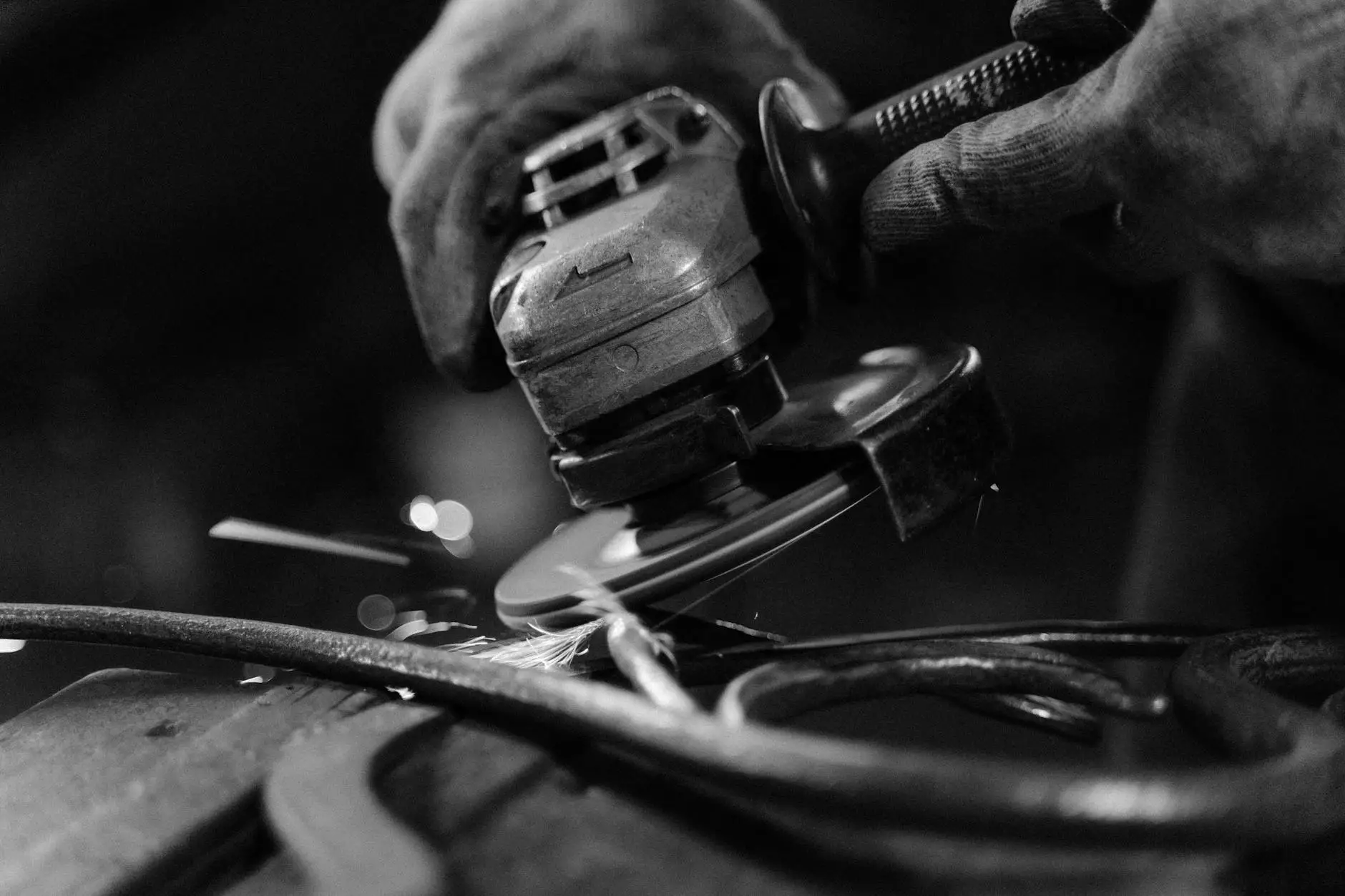
The world of manufacturing is constantly evolving, shaped by advancements in technology and increasing demand for precision and efficiency. At the forefront of this revolution are CNC precision machining suppliers, who play a pivotal role in delivering high-quality components for various industries. This article delves deep into the realm of CNC precision machining, exploring the qualities that define exceptional suppliers, and outlining the benefits they offer to businesses like those presented on deepmould.net.
What is CNC Precision Machining?
CNC (Computer Numerical Control) precision machining is a manufacturing process that utilizes computer-controlled machines to produce parts and components with high accuracy. This technology enables manufacturers to create intricate shapes and designs that would be difficult, if not impossible, to achieve with traditional machining methods.
Core Principles of CNC Machining
- Automation: CNC machines operate automatically, reducing the need for direct human intervention, which minimizes errors and enhances efficiency.
- Precision: With the aid of computer programs, CNC machines can achieve tolerances of up to +/- 0.001 inches, making them ideal for industries that require extreme precision.
- Repetition: Once programmed, CNC machines can reproduce the same part multiple times, ensuring consistent quality across batches.
The Role of CNC Precision Machining Suppliers
CNC precision machining suppliers are specialized entities that provide the machines, tools, and expertise necessary to carry out CNC machining processes. These suppliers serve a wide range of industries, including automotive, aerospace, medical, and consumer goods. Here are some key functions they perform:
1. Quality Assurance
One of the primary responsibilities of CNC precision machining suppliers is to maintain a strict quality assurance program. This includes rigorous testing and inspection protocols to ensure that every part meets the necessary specifications and standards. Suppliers often employ advanced measuring tools and quality control techniques to monitor their processes and outputs.
2. Customized Solutions
Every business has unique requirements, and top CNC precision machining suppliers recognize the importance of offering customized solutions tailored to individual client needs. This could involve modifying existing designs or creating entirely new parts based on specific criteria. Suppliers work closely with their clients to understand their operations and provide bespoke services that enhance productivity.
3. Advanced Technologies
The best CNC precision machining suppliers invest in cutting-edge technologies to stay ahead of the competition. This includes utilizing state-of-the-art software for design and simulation, as well as adopting high-speed machining equipment that boosts productivity and reduces lead times.
Benefits of Partnering with CNC Precision Machining Suppliers
Choosing the right CNC precision machining supplier can have a profound impact on a company's operational efficiency and product quality. Here are several benefits to consider:
1. Cost Efficiency
By collaborating with skilled suppliers, businesses can reduce production costs significantly. With the automations provided by CNC machines, labor costs decrease, and raw material waste is minimized due to the precision of machining processes. In the long run, this translates to lower overhead expenses and increased profit margins.
2. Rapid Prototyping
Many CNC precision machining companies offer rapid prototyping services, allowing businesses to quickly develop and test their product designs. This accelerates the product development cycle, enabling companies to bring their products to market faster and stay competitive.
3. Enhanced Design Flexibility
Modern CNC machines are capable of handling complex geometries and intricate designs, which means businesses can pursue innovative designs without worrying about manufacturing constraints. This flexibility allows for greater creativity in product development.
4. Scalability
CNC machining can easily scale to meet changing production demands. Whether a company needs to produce a small volume of parts or increase output significantly, reputable CNC precision machining suppliers can adjust their capabilities to match those needs while ensuring consistent quality.
Key Considerations When Selecting CNC Precision Machining Suppliers
1. Experience and Reputation
A supplier's industry experience is crucial. Established suppliers often have a proven track record of successfully delivering quality parts. Look for reviews, testimonials, and case studies to gauge a supplier's reputation in the market.
2. Technological Capabilities
Different suppliers may employ varying technologies and equipment. It is important to assess whether a potential supplier's capabilities align with your specific needs. Advanced machining centers and software can significantly impact production quality and efficiency.
3. Certifications
Certifications such as ISO 9001 indicate that a supplier adheres to recognized quality management standards. Working with certified CNC precision machining suppliers can provide peace of mind regarding the quality of the products they deliver.
4. Customer Service
Exceptional customer service is a vital aspect of any successful business relationship. Suppliers should demonstrate a commitment to effective communication, timely responses, and a willingness to collaborate closely with clients throughout the machining process.
Future Trends in CNC Precision Machining
The CNC precision machining industry is poised for continued innovation. Some key trends to watch for include:
1. Increased Automation and AI Integration
The integration of AI and machine learning into CNC machines will enhance their capabilities, allowing operators to predict maintenance needs, optimize production schedules, and enhance precision further. This will lead to even lower operational risks and improved cycle times.
2. Sustainable Practices
With growing environmental awareness, CNC suppliers are increasingly adopting sustainable practices, including energy-efficient machines, recycling waste materials, and using green manufacturing techniques. Businesses must consider sustainable processes when choosing suppliers.
3. Customization through 3D Printing
As 3D printing technology evolves, suppliers may offer integrated services that combine CNC machining with additive manufacturing to provide unique and complex components effectively. This hybrid approach allows for unprecedented design freedom.
Conclusion: The Competitive Edge of CNC Precision Machining Suppliers
In summary, CNC precision machining suppliers are essential partners in modern manufacturing, enabling companies to meet the challenges of today's competitive landscape. By providing quality assurance, customized solutions, and advanced technologies, these suppliers help businesses achieve efficiency, cost reductions, and greater design flexibility.
As the industry continues to evolve with technological advancements and increased demands for sustainability, businesses that proactively engage with reliable CNC precision machining suppliers are likely to gain a competitive edge. Choosing the right supplier can empower manufacturers to innovate, enhance product offerings, and secure a successful and prosperous future.